The world of printing has undergone a revolutionary transformation in recent years, thanks to the emergence of multi-material 3D printing technology. This innovative approach to printing has the potential to disrupt traditional manufacturing processes and open up a world of possibilities in various industries, including aerospace engineering, medical printing, and sustainable architecture.
With the ability to incorporate multiple materials into a single printed object, multi-material 3D printing offers increased functionality, reduced assembly time, design freedom, and improved performance.
Advantages of Multi-Material Printing
Multi-material 3D printing is a groundbreaking technology rapidly transforming the manufacturing landscape. Unlike traditional single-material printing, it allows for the incorporation of diverse materials within a single printed object. This unlocks a treasure trove of advantages that are significantly impacting various industries.
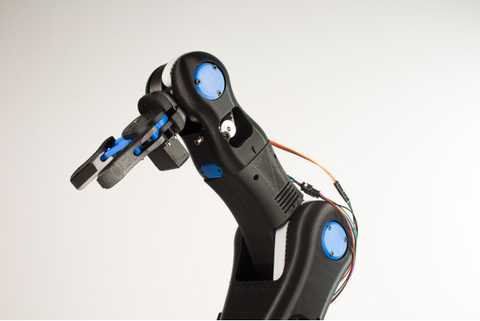
One of the most significant advantages is the ability to create objects with improved functionality. Imagine a gripper for a robotic arm, by combining a rigid material for the base with a soft, flexible material for the gripping surface, multi-material printing can achieve this complex functionality in one go. This eliminates the need for separate components and complex assembly processes.
Furthermore, multi-material printing offers a dramatic reduction in assembly time. Previously, intricate objects required the printing and subsequent assembly of multiple parts. With multi-material printing, these objects can be printed complete in a single run, streamlining the entire manufacturing process. This translates to significant time and cost savings for businesses.
The benefits extend beyond just efficiency. Multi-material printing empowers designers to create objects with tailored properties. For example, the aerospace industry can leverage this technology to print lightweight aircraft components with varying stiffness levels for optimal performance. Similarly, the medical field can create personalized medical implants by combining rigid materials for structural integrity with flexible materials for patient comfort. This level of customization paves the way for groundbreaking advancements in various sectors.
What is currently available in the Market
Bambu Lab AMS
Bambu Lab's Automated Material System (AMS) takes multi-material printing to a whole new level. This upgrade, compatible with P1P and Carbon printers, allows you to use up to four spools of filament simultaneously. If you're feeling truly adventurous, and have a full AMS setup with the hub, you can utilize a mind-blowing 16 different filaments in a single print!
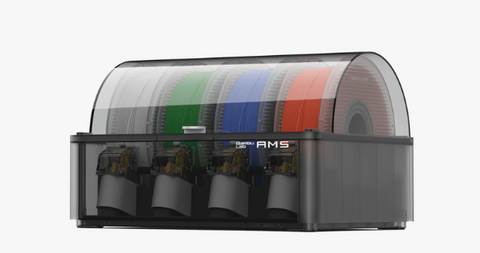
It's important to note that the AMS is currently exclusive to Bambu Lab printers. While this might be limiting for those with different brands, the seamless integration with P1P and Carbon makes setup a breeze. For those seeking a more compact option, the A1 Mini offers compatibility with the AMS Lite. However, keep in mind that neither AMS version is currently compatible with flexible filaments.
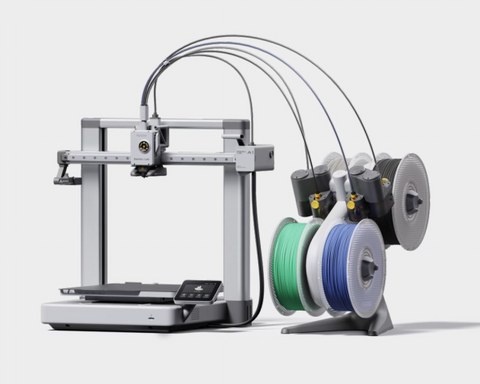
Material changes are handled through a clever purging system. Instead of a bulky block, the AMS uses small filament threads to transition between materials, minimizing waste. Overall, the quality and capabilities of the AMS are undeniable, making it a compelling option for those seeking advanced multi-material printing with Bambu Lab machines.
Mosaic Palette
This ingenious accessory dethrones limitations, working with most FDM printers to unleash the power of eight-material printing. Imagine a chameleon of a filament, seamlessly transforming between colors, textures, and properties within a single print.
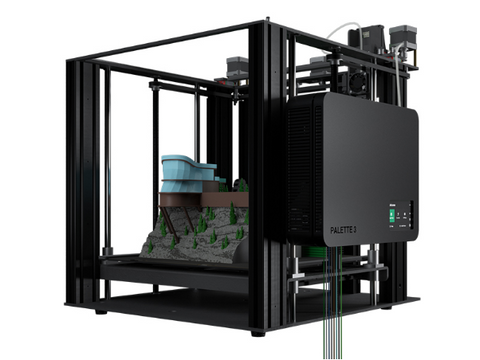
The magic lies in Mosaic's splicing technology. It acts like a filament conductor, precisely chopping and fusing various materials into a single strand. Your printer then treats it like any other filament, ready to bring your multi-material visions to life. The latest iteration boasts faster printing speeds and an "auto-refill" feature that keeps the printing uninterrupted – no more scrambling to swap spools mid-print.
However, the Palette isn't without its quirks. Similar to other multi-material systems, it utilizes a "purge block" to transition between materials, and this can lead to some waste. But Mosaic isn't afraid to get its hands dirty (metaphorically, of course). Their Canvas slicing software empowers you to fight back against waste. You can now calibrate the purge amount between specific materials, essentially minimizing the sacrifice. Plus, the software even allows you to incorporate some of the purged material into your print's infill – a clever way to turn potential waste into functional strength.
Prusa XL
Forget single-material limitations. The Prusa XL rewrites the rules of multi-material printing. This powerhouse boasts a unique tool changer system, capable of housing up to five independent extruders. Imagine the possibilities: printing objects with a symphony of materials, seamlessly blending rigid and flexible components, or incorporating dissolvable support structures without breaking a sweat.
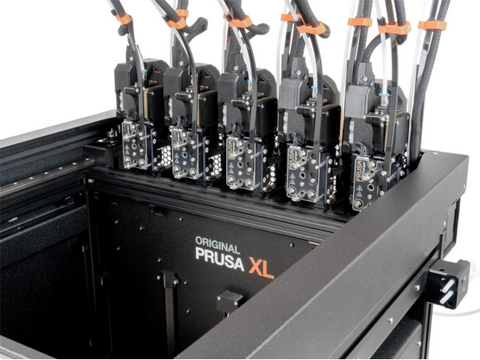
The XL unlocks a new level of design freedom, allowing you to craft objects with intricate details and varying functionalities – all within a single print. No more cobbling together parts from different materials; the XL lets you create complex masterpieces directly from your imagination.
Challenges and Limitations
While multi-material 3D printing has undoubtedly revolutionized various industries, like any emerging technology, it does come with its fair share of challenges and limitations. In this section, we will explore some of these hurdles and highlight how manufacturers and researchers are addressing them.
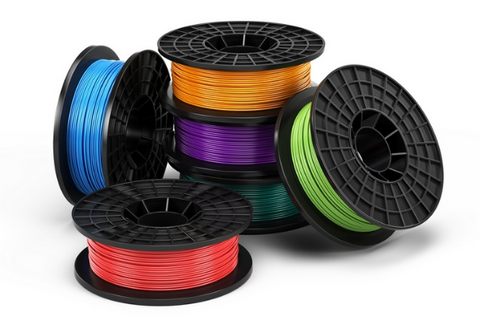
One of the primary challenges of multi-material 3D printing is the need for compatible materials. Each material used in the printing process must be able to adhere to and bond with the other materials, ensuring a strong and reliable final product. Achieving compatibility between different materials can be a complex task, requiring precise control over factors such as temperature, viscosity, and curing time.
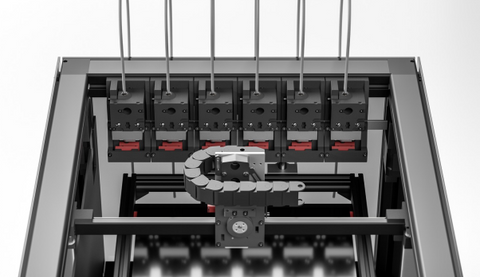
Another limitation of multi-material 3D printing is the complexity of the printing process itself. Printing with multiple materials often involves more intricate machinery and software, increasing the overall complexity and cost of the system. This can be a significant barrier for smaller businesses or individuals looking to adopt this technology.
Furthermore, the scalability of multi-material 3D printing is a challenge that needs to be addressed. While the technology has proven successful in producing small-scale prototypes and custom-made products, scaling up the production to meet larger demand can be a daunting task. Manufacturers are constantly exploring ways to optimize and streamline the printing process to unlock its full potential for mass production.
Despite these challenges, significant progress is being made to address the limitations of multi-material 3D printing. Researchers are constantly developing new materials with enhanced compatibility and experimenting with novel printing techniques to simplify the process. Additionally, advancements in automation and software technology are making the printing process more efficient and cost-effective.
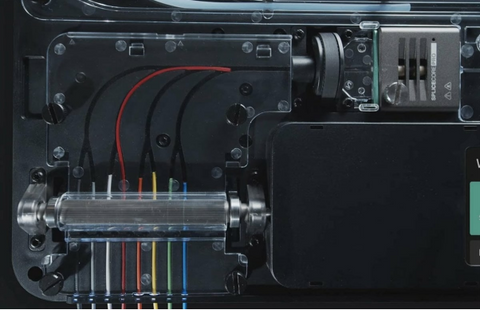
Multi-material 3D printing isn't just a technological marvel, it's a gateway to a future brimming with possibilities. Imagine a world where intricate medical implants, perfectly customized for individual needs, roll off printers with ease. Picture lightweight aircraft components, boasting both strength and flexibility, soaring through the skies.
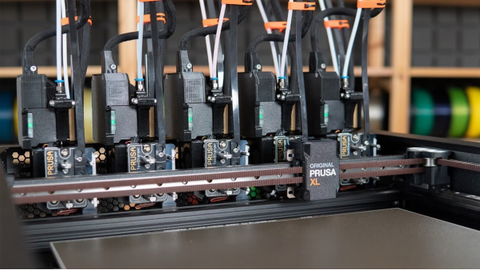
Of course, challenges remain. Material compatibility can feel like a constant puzzle, and scaling up production for mass markets requires innovative solutions. But with each hurdle overcome, with each new material combination explored, the potential of multi-material printing unfolds a little further.